Revealing the Core of Electronic Products: How are circuit boards manufactured?
In the world of electronic products, circuit boards are known as the "mother of electronic products". It carries various complex circuits and components, which is the key to the normal operation of electronic products. So, how was this magical circuit board made? Next, let's enter the mysterious world of circuit board manufacturing together.
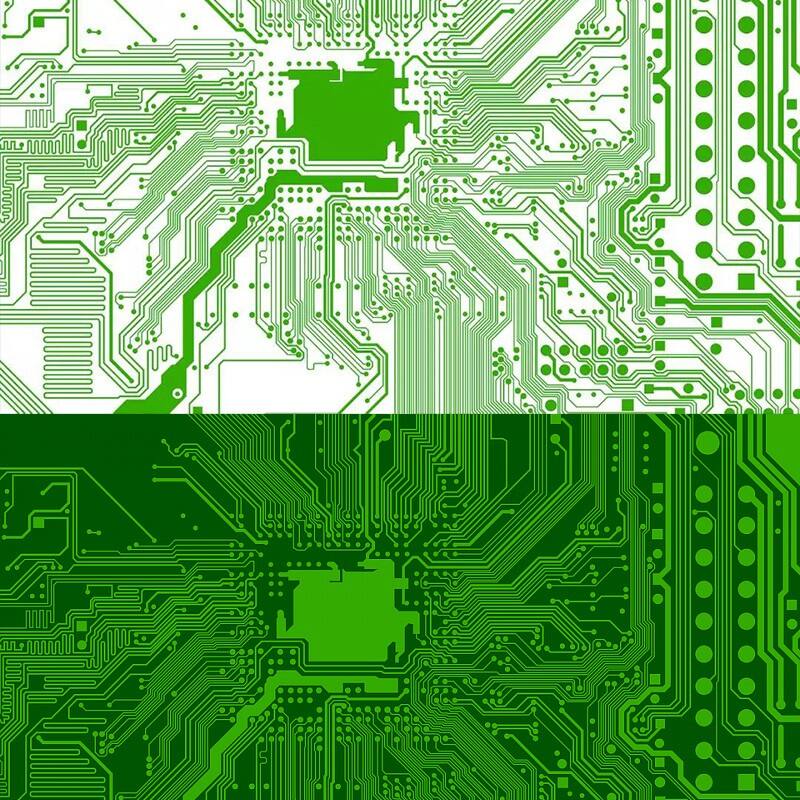
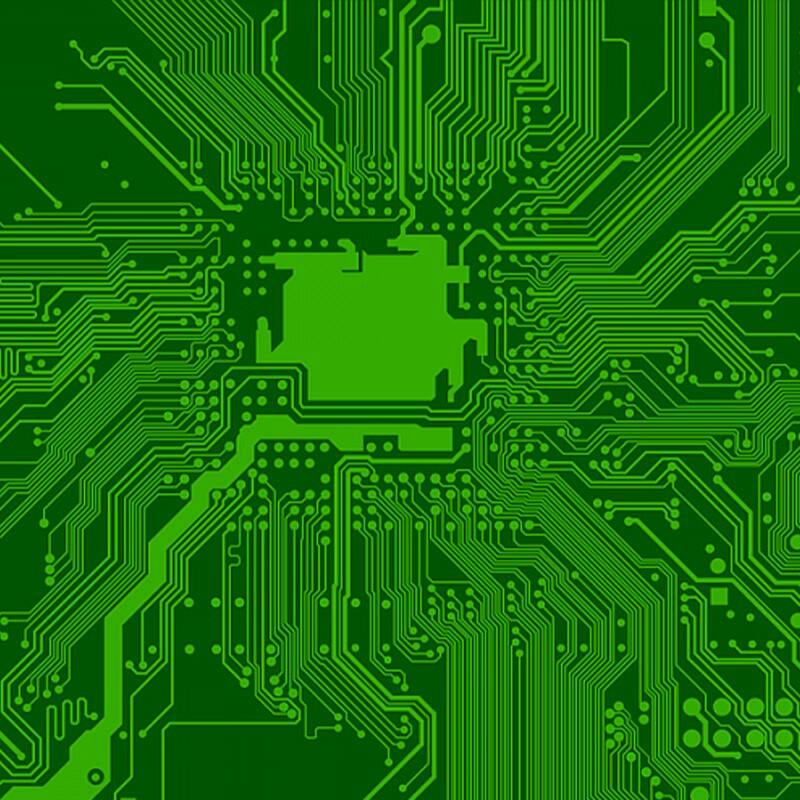
1、 Design and Layout
The manufacturing of circuit boards starts with design. The designer draws a detailed circuit diagram based on the usage principles and parameters of the product. Then, using professional design software, convert the circuit diagram into layout and wiring design for the circuit board. This step is the foundation of circuit board manufacturing, determining the functionality and performance of the circuit board.
2、 Preparation of raw materials
The main raw material for circuit boards is glass fiber epoxy resin material, which is covered with copper plates on both sides. According to design requirements, these raw materials will be cut into appropriate sizes to prepare for subsequent processing.
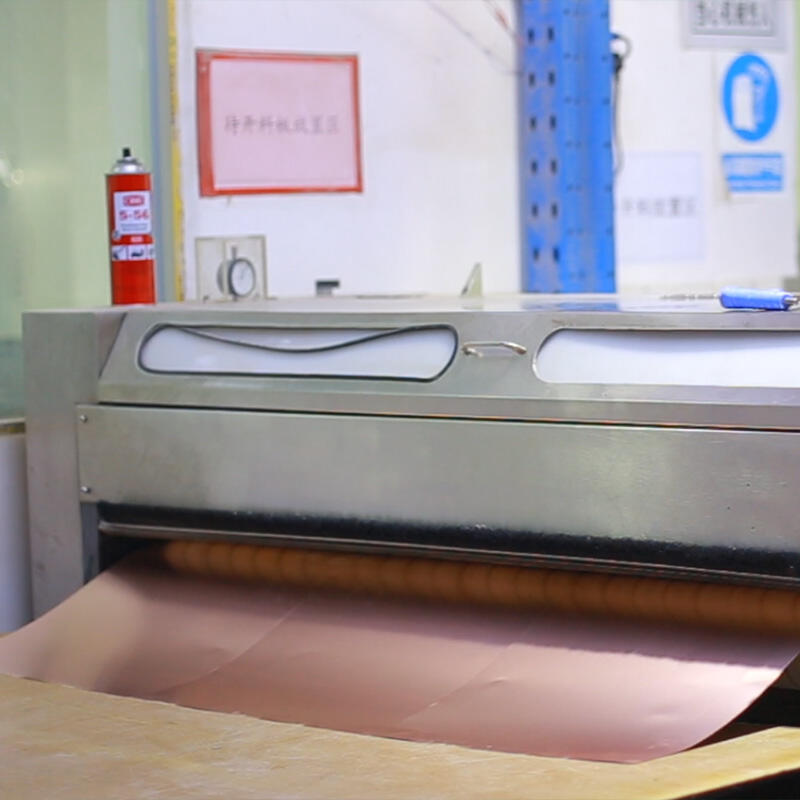
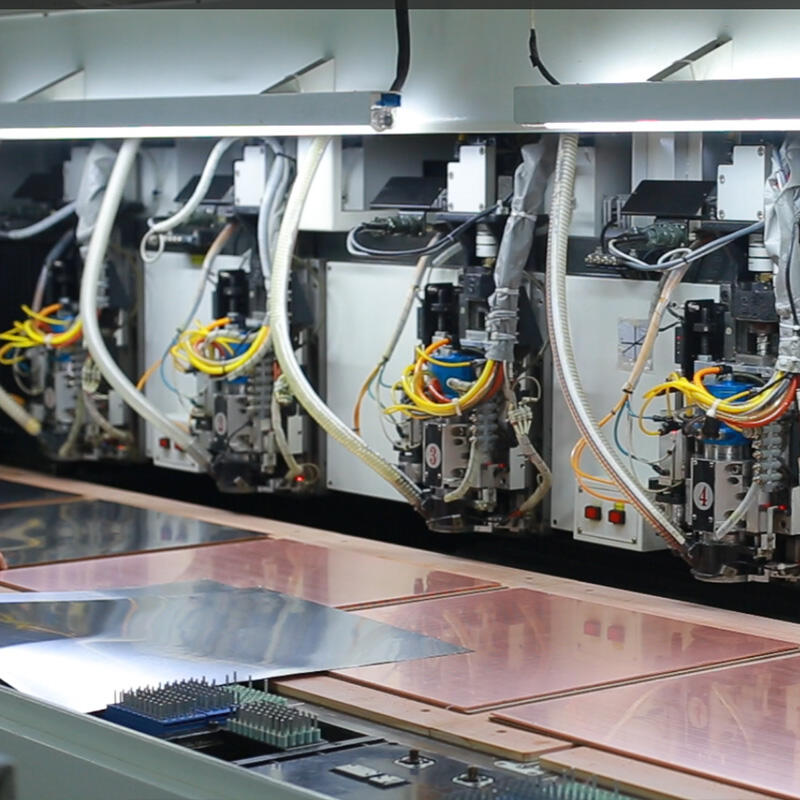
3、 Create circuit patterns
On the copper plate, a layer of dry film (a material sensitive to ultraviolet radiation) is covered and exposed using a photo mask with circuit patterns. In this way, only the dry film of the circuit part will undergo polymerization reaction and solidification, while the other parts will be dissolved. Next, through the etching process, the uncured copper plate is partially dissolved, leaving only the designed circuit pattern.
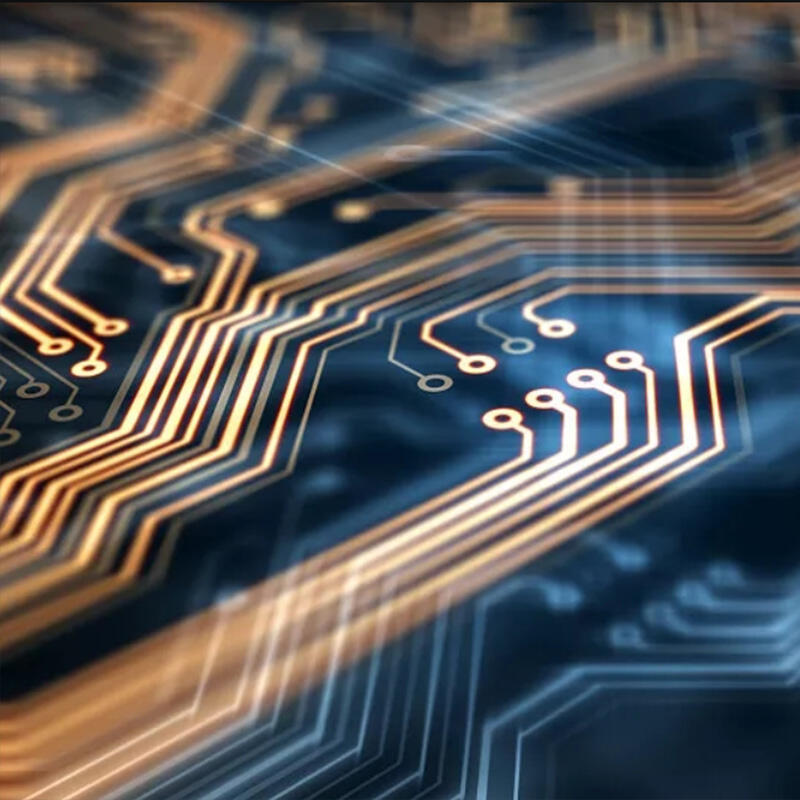
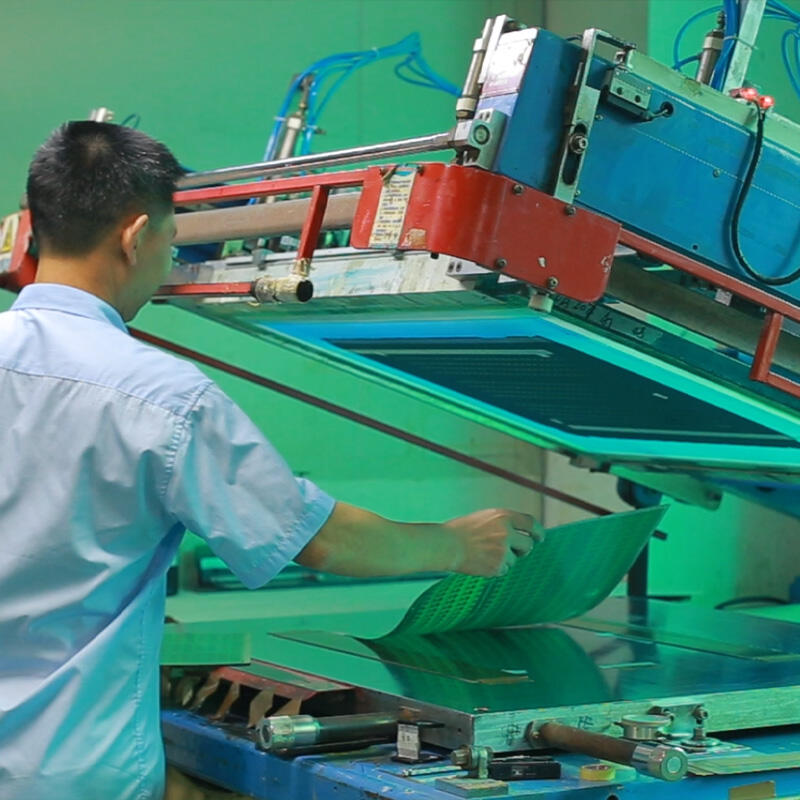
4、 Manufacturing of multi-layer circuit boards
For complex electronic products, multi-layer circuit boards are required. This is achieved by stacking multiple layers of circuit boards and using high-temperature and high-pressure machines for lamination. After the lamination is completed, drilling and copper plating processes are also required to ensure that the circuits between different layers can be connected.
5、 Protection circuit
To protect the circuit board from external environmental influences, it is necessary to apply a layer of solder mask ink on its surface. However, in order to facilitate the installation of components, it is necessary to remove ink from the areas where the components come into contact. This is also achieved through exposure and development processes.
6、 Installing components
After the circuit board is completed, it is necessary to start installing the components. This process is mainly completed by machines, including applying solder paste to the welding points, automatically placing components, and melting and solidifying the solder paste through an oven. Finally, the components and circuit board are tightly soldered together to form a complete circuit board assembly.
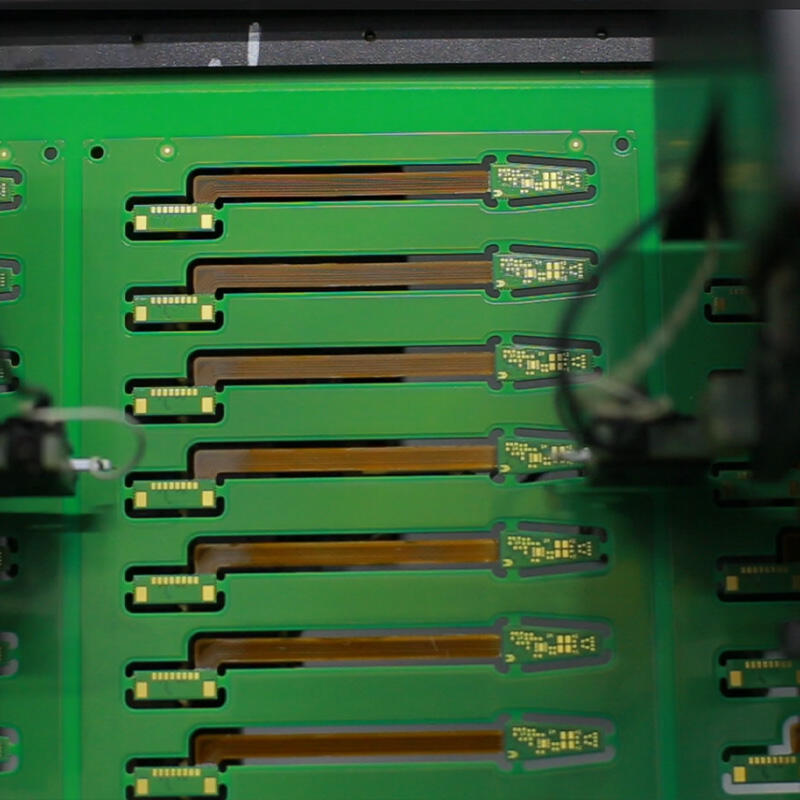
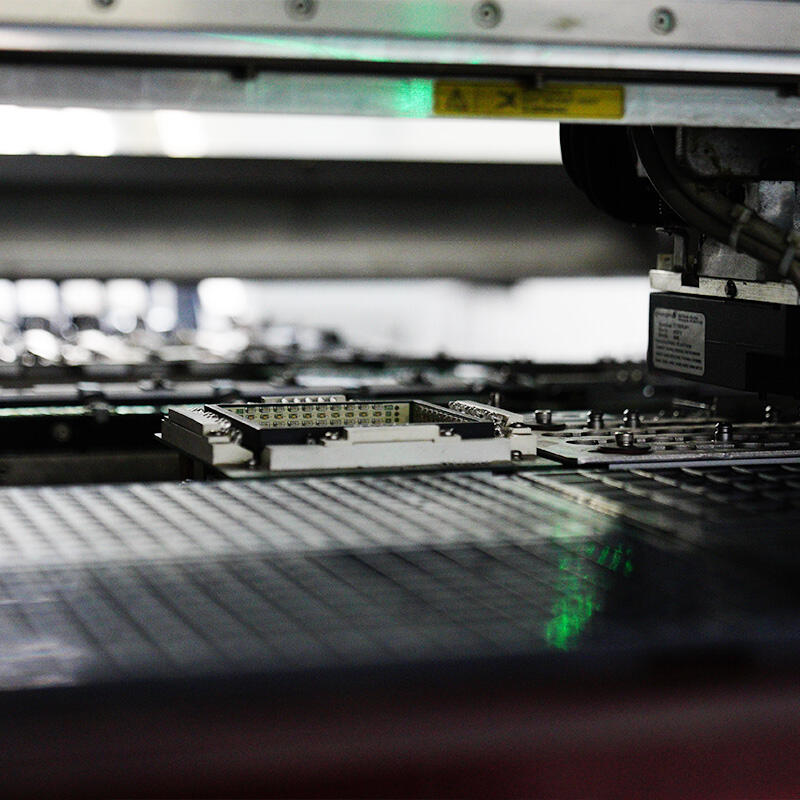
7、 Testing and Packaging
After installing the components, it is necessary to test the circuit board to ensure its normal performance. After passing the test, the circuit board can be packaged and delivered to the customer.
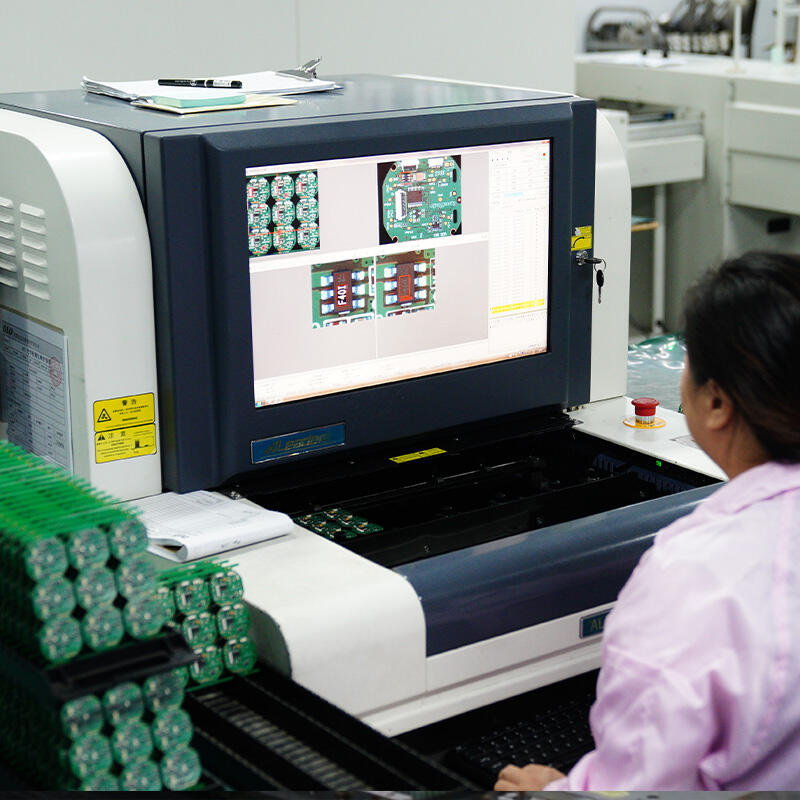
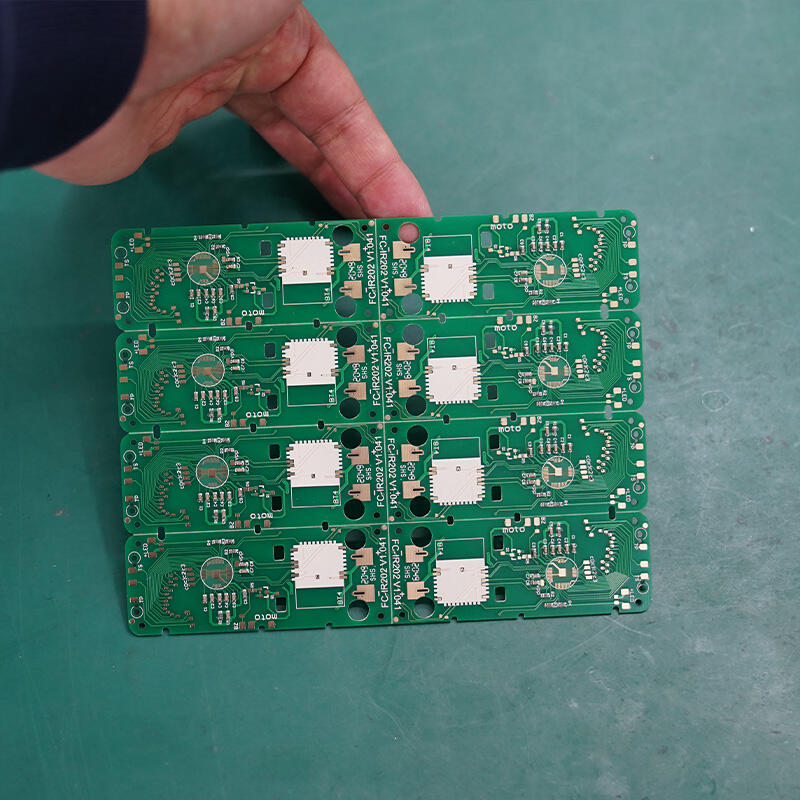
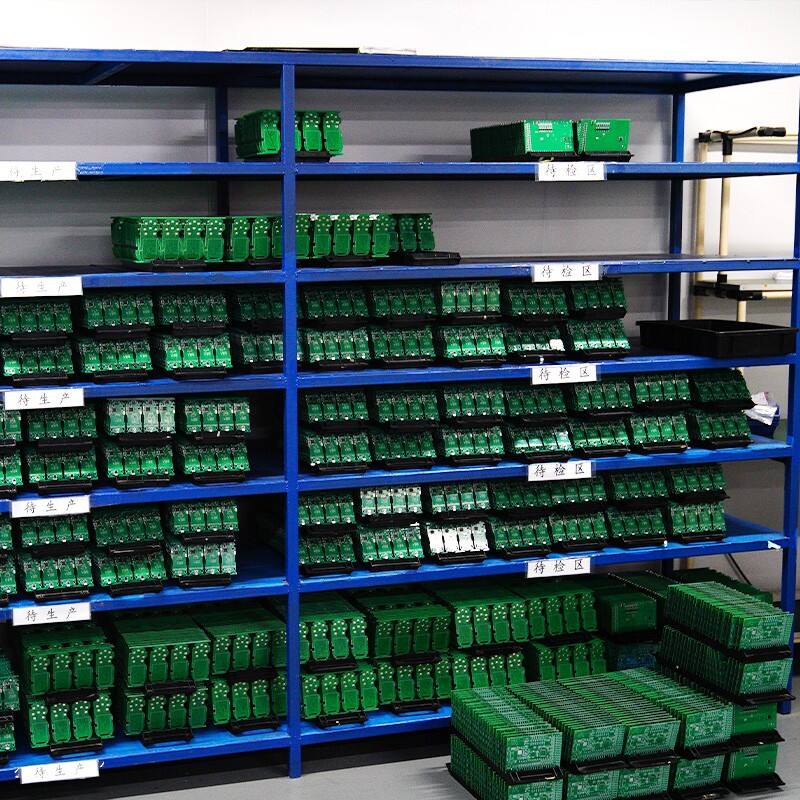
By following the above steps, a complete circuit board has been manufactured. It carries the core functions of electronic products and is an indispensable and important component of electronic products.
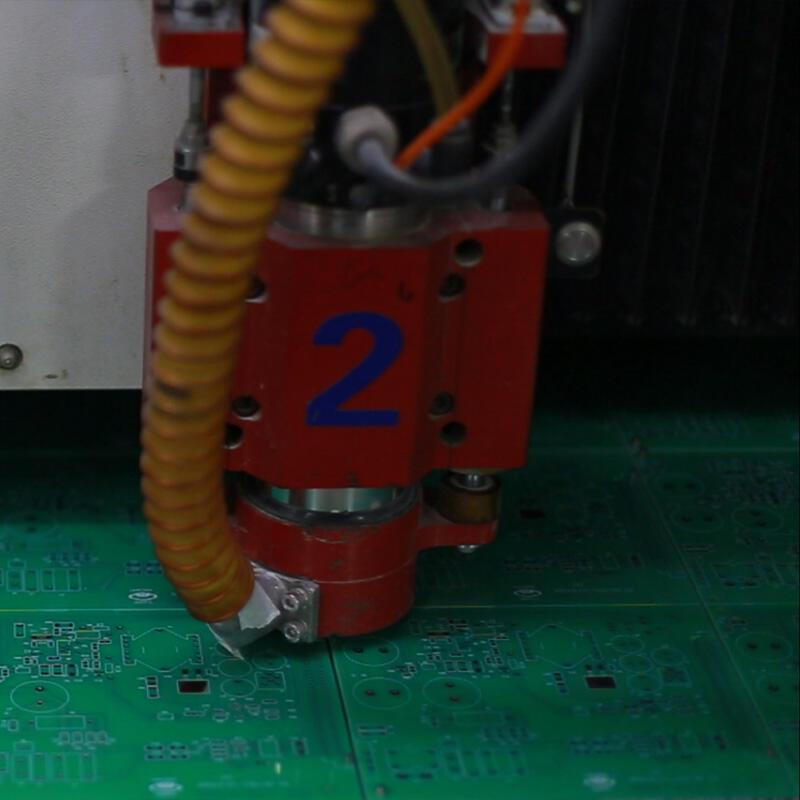
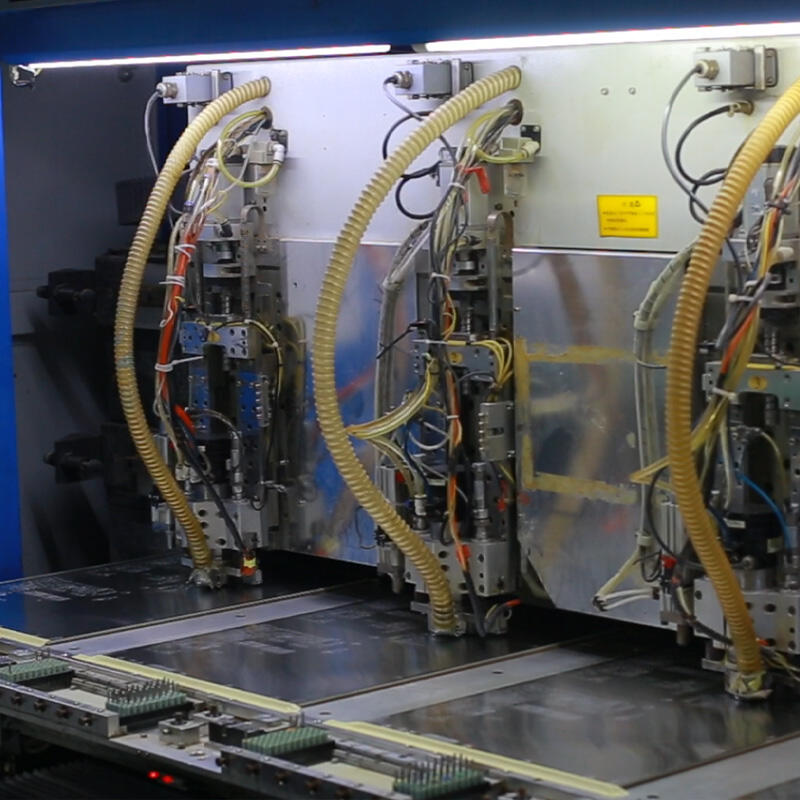